Trump’s tariffs are intended to give U.S. manufacturing a boost. Is it ready?
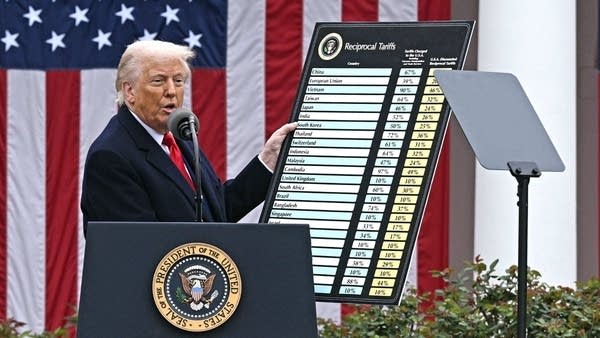
President Donald Trump announced sweeping tariffs of at least 10% on practically all goods coming into the United States on Wednesday. Many countries, along with the European Union, promised to respond with sanctions of their own.
One of the president’s goals with all these tariffs is to get more companies to make more products here in the U.S. To do that, many would need to build new factories and hire a whole lot of people to work at those factories.
But are there enough workers with the right skills to fill all those potential new manufacturing jobs? The United States once led the world in manufacturing. These days, China does.
But Willy Shih, a professor at Harvard Business School, said we still make plenty of things.
“We do have a large auto industry, we do do vehicle assembly,” he said.
So it wouldn’t be hard to make even more cars here, he said. The workforce already exists.
But there are lots of other things that we don’t make much of in the U.S., like semiconductor chips.
“Some of the most advanced packaging in semiconductors requires things like advanced ceramics,” Shih said. “We lost those skills, or actually, especially for some of the newer materials, we never developed those skills in the first place.”
That’s true of other high-tech products too, said Ben Armstrong at the Massachusetts Institute of Technology’s Industrial Performance Center.
“Things like magnets, which are really critical for batteries and other core electronic technologies. We’ve really lost the capacity to build in the U.S.,” he said.
Armstrong said it’s possible to build that capacity here, either again or from scratch. “But it takes a long time, and it takes really significant investment,” likely from the government and from companies.
They’ll need to recruit and train thousands of workers in new kinds of manufacturing.
“What they often do is they bring people who are experts from where they’re based, often in Asia, and they come to the U.S. to train this new workforce and get them up to speed,” he said. “This is a yearslong process.”
There is already some infrastructure for large-scale workforce development, said Arthur Wheaton, director of labor studies at Cornell University’s School of Industrial and Labor Relations.
“You have unions … a lot of them have apprenticeship programs that are designed already … and partnerships with community colleges across the country have been very beneficial,” he said.
But, he said, companies will probably wait until U.S. policy is clear to make a move.
“The tariffs would need to be in place for an extended period of time with some expectation that they won’t change,” Wheaton said, for companies to feel like it’s worth investing in workforce development, and for workers to feel like it’s worth training for those jobs.